Ein hoffentlich fiktiver Nachruf auf die „deutsche" Industrie 4.0 aus dem Jahr 2020 und ein zukunftsoptimistisches Vorwort
Winfried Felser, Competence-Site.de, Martin Hofer, Wassermann AG
Vorwort:
Der folgende Nachruf ist natürlich fiktiv, aber vielleicht sollten wir hier und heute nach vorne in das Jahr 2020 und dann zurückblicken, um jetzt die richtigen Weichen zu stellen bzw. zu erkennen, welche Weichen vielleicht noch nicht ideal gestellt sind. Dabei sind beide Autoren Verfechter des Industrie-4.0-Weges und so soll der Nachruf auch kein Spottwerk sein, sondern aufrütteln.
Die Wassermann AG und ihre Kunden machen sich jedes Jahr auf diesen Weg in Richtung einer kollaborativeren Industrie auf der Basis der Digitalisierung und Vernetzung, demnächst wieder auf den Vision-Days 2015 mit dem Schwerpunkt Industrie 4.0. Und auch die Competence Site hat mit Priorität das Competence Book Industrie 4.0 realisiert, um einen kleinen Beitrag zu leisten. Insofern: Wir glauben an Industrie 4.0 und sehen den Nachruf als Anregung, die unserem gemeinsamen Industrie-4.0-Erfolg dienen soll. In diesem Sinne.
Liebe Freunde der Industrie 4.0,
heute, am 31.12.2020 nehmen wir in großer Trauer Abschied von einem großen Talent, das mit großen Ambitionen spätestens seit April 2013 (Abschlussbericht des Arbeitskreises Industrie 4.0) durchstarten sollte: die „deutsche" Industrie 4.0.
2013 war eigentlich alles perfekt für den nachhaltigen Erfolg dieses Projekts vorbereitet. Der Abschlussbericht des Arbeitskreises Industrie 4.0 war ein fundierter Wegweiser. Die Industrie in Deutschland war zudem immer noch der Schlüsselfaktor für unseren ökonomischen Erfolg, das versprach entsprechende Relevanz des Themas für alle Beteiligten, auch auf politischer Ebene.
Gerade Deutschland verfügte zugleich über hervorragende Kompetenzen für ein Gelingen von Industrie 4.0. Neben den bekannten und Hidden Champions in der Industrie, war auch die industrienahe Informationstechnologie aus Deutschland führend (ERP-, MES-, APS-Systeme).
![2014-10-17-grafik1.png]()
Diskussion zu Industrie 4.0, s. Video (Bild G+F Verlags- und Beratungs- GmbH)
Nicht nur Konzerne wie Siemens und SAP, sondern auch mittelständische Unternehmen wie z. B. Phoenix Contact oder Wassermann standen für Kompetenz im Bereich der Produktionstechnologie und des Produktionsmanagements. Dass sich zudem die Verbände VDMA, BITKOM und ZVEI zur Plattform Industrie 4.0 (kooperativ!) zusammenschlossen und auch andere Verbände wie VDI oder DSAG das Vorhaben unterstützten, war vielversprechend.
Wie konnte es trotz allem dazu kommen, dass Deutschlands ambitioniertestes und vielleicht auch zukunftswichtigstes Projekt nicht den gewünschten Erfolg brachte? Nun, sieben Jahre später, im Jahr 2020, wird Deutschlands Industrie 4.0 Teil des erfolgreicheren „Industrial Internet Consortiums" (IIC), das einst von Schlachtschiffen wie General Electric, CISCO, IBM und Intel in den USA gegründet wurde, aber heute Unternehmen aus allen Ländern umfasst?
Wieso haben wir im Ergebnis nicht die Ziele einer umfassenden und vor allem führenden Transformation unserer Industrie und ihrer Partner erreicht, die wir eigentlich angestrebt haben?
Die Gründe dafür waren sicherlich vielfältig, jede finale Erklärung wird unzureichend sein, trotzdem wollen wir heute im Rückblick eine Analyse wagen. Zum einen überließen uns bereits 2013 die globalen Wettbewerber das Zukunftsfeld nicht einfach kampflos. Ein globaler Erfolg eines „deutschen" Konzepts war von Anfang an eine große Herausforderung zwischen dem schnellen Agieren der Großen (und trotzdem Schnellen) aus dem Silicon Valley und der schieren Investitions-Power Chinas, einem Land, das nicht mehr nur verlängerte Werkbank sein wollte.
So investierten z. B. 2013 die USA unter der Obama-Administration allein für die Produktionsforschung 1,6 Mrd. Euro und bereits 2012 starteten Programme wie das „Advanced Manufacturing Partnership". Im Rahmen dieses Programms wurden regionale Kompetenzzentren im Bereich Fertigung eingerichtet, um die an den Universitäten entwickelten Zukunftstechnologien auch in der Praxis einsetzen zu können.
Diese Programme ergänzen forschungsseitig, was industrieseitig durch das IIC und andere Netzwerke realisiert wurde. Neben General Electric und Cisco (Gründer des IIC) entdeckten zudem die Marktführer des Silicon Valleys zunehmend die Industrie als Betätigungsfeld (es fing alles klein an, z. B. mit der Akquisition von NEST- und einigen Roboter-Firmen durch Google).
![2014-10-17-Grafik2.png]()
Produktionsmaschinen, die das Twittern lernen siehe Beitrag (Bild: istockphoto)
Lange Zeit wurden die Player aufgrund ihrer Herkunft aus dem Consumer-Bereich von den etablierten Herstellern verdrängt, obwohl bei Google, Apple und anderen früh die Ambition in Richtung Industrie erkennbar war. „Software frisst den Rest der Welt" verkündete Marc Andreessen schon viele Jahre zuvor und er meinte damit nicht nur den Consumer-Bereich.
Schon im Jahr 2014 kamen daher auch wichtige Zukunftsimpulse wie die „twitternden" Produktionsmaschinen (auf Basis von MTConnect) aus den USA. Als in Deutschland noch die Standardisierungsgremien tagten, wurden aus den USA kommend de facto also bereits wichtige „Claims" besetzt. Dass Deutschland in den Jahren zuvor Schlüssel-Kompetenzen z. B. im Bereich der mobilen Kommunikation (Siemens) abgebaut hatte, war dabei sicherlich nicht hilfreich.
Auch China und der Rest der Welt waren aber nicht untätig und so gingen nicht nur Google & Co auf Einkaufstour. China plante 2014 für drei Jahre für die Modernisierung und Transformation der chinesischen Industrie mit Investitionen von 1,2 Billionen Euro. China wollte nicht länger nur die verlängerte Werkbank sein. Aus dem alten „Made in China" sollte nun „Created in China" werden.
Dass China in den folgenden Jahren führende deutsche, mittelständische Unternehmen aufkaufte, war da nur konsequent. So warnten 2014 auch bereits international agierende Vordenker wie Professor Sachsenmeier vor den Mythen der Industrie 4.0 und führten in Bezug auf China aus in einem Interview mit der Competence Site aus:
„In China wird sich Quantität zunehmend zu Qualität verwandeln, einfach, weil die Beschäftigung mit Produktion zu immer besseren Kenntnissen führt. Da diese Kenntnisse anderswo abgebaut werden, werden viele industrielle Bereiche Chinas über Zeit zu weltweit führenden Exzellenzclustern werden. Hochflexible Massenfertigung zeichnet China heute schon aus; das fokussierte Herstellen von Sonderanfertigungen ist da nicht weit."
International agierende Experten wie er warnten zudem davor, neben den USA und China andere Player zu vernachlässigen. Indien war schon damals als Markt und Informatikpool enorm wichtig. 2014 alarmierte Sachsenmeier daher zukunftsweisend in dem Interview mit der Competence Site:
„Dort werden Produkte und Dienstleistungen für hunderte von Millionen Menschen hergestellt... zu unschlagbaren Konditionen. Die damit verbundenen Lernkurven machen Indien wettbewerbsstark, wir werden es nur nicht gleich merken."
Damit war der eigene Erfolg für das deutsche Projekt „Industrie 4.0" im globalen Wettbewerb zumindest kein Selbstläufer. Es war von vorneherein klar, dass andere nicht nur zuschauen würden.
Zum anderen scheiterte Deutschland aber an hausgemachten Problemen. Was aber genau lief schief? In erster Linie scheiterte Deutschland an den Herausforderungen der deutschen Innovations-DNA und strategischen Weichenstellungen.
Unvermeidbare Herausforderungen der deutschen Innovations-DNA waren:
• Die zu geringe Marktorientierung:
Forschung („Theorie") vs. Markterfolge („Umsatz")
• Die zu geringe Nachfrageorientierung:
Angebotsorientierung (neue Lösung) vs. Nachfrageorientierung (wofür?)
• Die zu ausgeprägte Komplexitäts-Neigung
Kompliziert („ganzheitlich") vs. einfach („KISS")
Strategische Weichenstellungen (de facto) gegen den Zukunftserfolg waren:
• Das falsche Paradigma:
Basistechnologie („RFID", „Google Glass", „IP") statt integrierte Systeme
• Die unzureichende Differenzierung:
Kein spezifisch „deutscher" Fokus! (z. B. Kollaboration statt Konkurrenz)
• Das ungenutzte Mittelstands-Potenzial:
Leuchttürme statt Breite des Mittelstands
Zu den Herausforderungen der deutschen Innovations-DNA:
Es scheint dem „deutschen Wesen" inhärent, dass wir tief bohren und neue, technisch anspruchsvolle Lösungen kreieren wollen. Das macht den Wettbewerb schwer mit Wettbewerbern, die ihren Markt und Markterfolg in den Vordergrund stellen und mit smarten Lösungen schnell voraus- oder nachlaufen.
So wird dann in Deutschland MP-3 entwickelt, aber erst in den USA wird die entsprechende Technologie auf der Basis neuer Geschäftsmodelle zum Milliardengeschäft. Die ersten drei Probleme sind also typisch „deutsch" bzw. Teil unserer deutschen Innovations-DNA, die uns andererseits oft nachhaltige, komplexe Lösungen schaffen lässt. Hiermit müssen wir also in gewisser Weise auch zukünftig leben.
Zu den strategischen Weichenstellungen gegen den Zukunftserfolg:
So wie die ersten drei Problemfelder fast zwangsweise unseren Erfolg erschwerten, hätten wir in den letzten drei Problemfeldern mit unseren „typisch" deutschen Voraussetzungen punkten können, wenn de facto die richtigen Weichenstellungen erfolgt wären.
Dabei waren prinzipiell diese Weichenstellungen bereits im Abschlussbericht vorhanden. Die tatsächlichen Weichenstellungen erfolgten dann aber durch die „real existierenden" Forschungs- und Förderungsschwerpunkte und die öffentliche Wahrnehmung des Projekts Industrie 4.0.
Betrachtet man die Gründer des IIC wie Intel oder CISCO, so stehen diese globalen Marktführer vor allem für Basistechnologien wie Computer-Chips und Netzwerke. Deutschlands erfolgreichstes IT-Unternehmen, SAP, war vor allem deshalb erfolgreich, weil die Gründer eine integrierte Unternehmenssoftware realisierten, mit der die früheren Insellösungen überwunden wurden.
Siemens punktete in seiner Historie auch immer wieder durch integrative Lösungen. Und auch sonst hatten Lösungen aus Deutschland insbesondere im Bereich der ERP-, MES- und APS-Systeme oft eine besondere „integrierende" Kompetenz.
Dabei sind „integrative" Lösungen nicht nur auf den unteren produktionsnahen Ebenen gefordert, sondern auch auf den höheren, planerischen Ebenen bzw. in der Vernetzung aller Ebenen.
Bei aller Begeisterung für RFID-Chips, Google Glass oder Kameras an Lagerbehältern: Oft steckt der Return on Investment der Industrie 4.0 eben eher in den vielen noch nicht genutzten Potenzialen einer besseren Prozess- und Planungsvernetzung als in den einzelnen Basistechnologien, die dafür vor allem Enabler sein sollten (und nicht technologischer Selbstzweck). Trotzdem wurde insbesondere in der öffentlichen Wahrnehmung zu wenig Integration und Planung betont, sondern eher die leichter kommunizierbaren technischen Lösungen.
![2014-10-17-Grafik3.jpg]()
Haus der Industrie 4.0 des VDI, siehe VDI-Blog (Bild: VDI)
Dieses „Technologie-zentrierte" Paradigma war dabei keineswegs alternativlos. So betonte beispielsweise das VDI-Haus eine integrierte Sicht auf Industrie 4.0 und mit der „Aachener Perspektive" der Kollaborationsproduktivität existierte paradigmatisch durchaus eine andere Herangehensweise an das Thema Industrie 4.0. Am FIR an der RWTH Aachen wurden frühzeitig der ROI und die Produktivität betont, die aus einer besseren Kollaboration durch Vernetzung und Integration dezentraler Intelligenz entstehen.
Man hätte dann global Basiskomponenten (China) und Kommunikations- und Computer-Infrastruktur (Intel, CISCO, ..., USA) nutzen und nachhaltig eine eigene integrative Wertschöpfungskompetenz ergänzen können.
Solche und andere Kollaborations- und Netzwerk-Paradigmen waren aber als Leitbilder nicht ausreichend prägend. Dabei wären gerade solche integrativen, kollaborativen Industrie-4.0-Paradigmen auch kompatibler mit unserer „deutschen" ökonomischen DNA der sozialen Marktwirtschaft gewesen. Deutschland steht in besonderer Weise für eine Ökonomie des Miteinanders, die Kooperations- statt reinem Konkurrenz-Denken betont.
Deshalb sind kooperative Strukturen wie Verbände so wichtig und so erfolgreich in Deutschland. Auf dieser Basis hätten wir unsere ökonomische DNA für eine Differenzierungsstrategie in Richtung eines Paradigmas Industrie 4.0 = höherer ROI durch bessere Integration und Kooperation nutzen können.
Mit dieser Perspektive wäre die „deutsche" Industrie 4.0 mehr gewesen als nur die in Deutschland angesiedelten Bemühungen bzw. der deutsche Begriff für Smart Factories bzw. Cyber Physical Systems. So aber fehlte die wichtige Differenzierung.
Gerade mit einer solchen differenzierenden Strategie hätten wir dann auch noch breiter bei den eigentlichen Trägern des deutschen Wirtschaftswunders punkten können, den mittelständischen Unternehmen.
Integrierte, kooperative Systeme für eine bessere Produktion und ein besseres Produktionsmanagement, das wäre ein spezifischer Fokus für die deutsche Rolle in der Digitalisierung der Industrie gewesen, die auch im Mittelstand populärer gewesen wären als ein technologischer Selbstzweck mit unklarem ROI.
Zugleich hätte man den Mittelstand mit Reifegrad- und Vorgehensmodellen da abholen müssen, wo er stand. Oft weist der Mittelstand bis heute noch nicht den Organisationsgrad und die Basis-Digitalisierung auf, die für eine Hightech-Version der Industrie 4.0 notwendig wären.
Bis heute sind viele Baustellen im Bereich Organisation, Prozesse und Planung zu suchen. Erst dann kann durch letzte Optimierungen der Basistechnologien gepunktet werden. Durch den Fokus auf führende Leuchttürme und Hightech-Lösungen wurde aber die Chance verpasst, unsere Stärke des Mittelstands in der Breite zu nutzen.
Leider wurden 2013, 2014, ... diese Fragen nach dem nachhaltigen Erfolg zu wenig beleuchtet. Jetzt sind wir im Jahr 2020 klüger und in Trauer. Vielleicht finden wir aber nun unseren Weg in den kommenden Jahren ohne ein nationales Label, aber mit spezifisch deutscher Kompetenz.
Wenn wir unsere DNA erkennen und die richtigen strategischen Weichenstellungen (richtiger Fokus, u. a. Marktorientierung, richtiges Paradigma, Mittelstandsorientierung, ...) vornehmen, dann sollte uns in Zukunft der Erfolg gelingen, selbst ohne einen nationalen Begriffsrahmen.
Winfried Felser, Competence-Site.de, Martin Hofer, Wassermann AG
Vorwort:
Der folgende Nachruf ist natürlich fiktiv, aber vielleicht sollten wir hier und heute nach vorne in das Jahr 2020 und dann zurückblicken, um jetzt die richtigen Weichen zu stellen bzw. zu erkennen, welche Weichen vielleicht noch nicht ideal gestellt sind. Dabei sind beide Autoren Verfechter des Industrie-4.0-Weges und so soll der Nachruf auch kein Spottwerk sein, sondern aufrütteln.
Die Wassermann AG und ihre Kunden machen sich jedes Jahr auf diesen Weg in Richtung einer kollaborativeren Industrie auf der Basis der Digitalisierung und Vernetzung, demnächst wieder auf den Vision-Days 2015 mit dem Schwerpunkt Industrie 4.0. Und auch die Competence Site hat mit Priorität das Competence Book Industrie 4.0 realisiert, um einen kleinen Beitrag zu leisten. Insofern: Wir glauben an Industrie 4.0 und sehen den Nachruf als Anregung, die unserem gemeinsamen Industrie-4.0-Erfolg dienen soll. In diesem Sinne.
Liebe Freunde der Industrie 4.0,
heute, am 31.12.2020 nehmen wir in großer Trauer Abschied von einem großen Talent, das mit großen Ambitionen spätestens seit April 2013 (Abschlussbericht des Arbeitskreises Industrie 4.0) durchstarten sollte: die „deutsche" Industrie 4.0.
2013 war eigentlich alles perfekt für den nachhaltigen Erfolg dieses Projekts vorbereitet. Der Abschlussbericht des Arbeitskreises Industrie 4.0 war ein fundierter Wegweiser. Die Industrie in Deutschland war zudem immer noch der Schlüsselfaktor für unseren ökonomischen Erfolg, das versprach entsprechende Relevanz des Themas für alle Beteiligten, auch auf politischer Ebene.
Gerade Deutschland verfügte zugleich über hervorragende Kompetenzen für ein Gelingen von Industrie 4.0. Neben den bekannten und Hidden Champions in der Industrie, war auch die industrienahe Informationstechnologie aus Deutschland führend (ERP-, MES-, APS-Systeme).
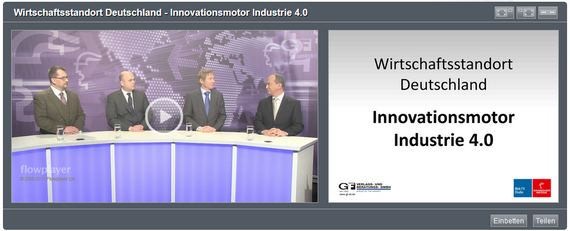
Diskussion zu Industrie 4.0, s. Video (Bild G+F Verlags- und Beratungs- GmbH)
Nicht nur Konzerne wie Siemens und SAP, sondern auch mittelständische Unternehmen wie z. B. Phoenix Contact oder Wassermann standen für Kompetenz im Bereich der Produktionstechnologie und des Produktionsmanagements. Dass sich zudem die Verbände VDMA, BITKOM und ZVEI zur Plattform Industrie 4.0 (kooperativ!) zusammenschlossen und auch andere Verbände wie VDI oder DSAG das Vorhaben unterstützten, war vielversprechend.
Wie konnte es trotz allem dazu kommen, dass Deutschlands ambitioniertestes und vielleicht auch zukunftswichtigstes Projekt nicht den gewünschten Erfolg brachte? Nun, sieben Jahre später, im Jahr 2020, wird Deutschlands Industrie 4.0 Teil des erfolgreicheren „Industrial Internet Consortiums" (IIC), das einst von Schlachtschiffen wie General Electric, CISCO, IBM und Intel in den USA gegründet wurde, aber heute Unternehmen aus allen Ländern umfasst?
Wieso haben wir im Ergebnis nicht die Ziele einer umfassenden und vor allem führenden Transformation unserer Industrie und ihrer Partner erreicht, die wir eigentlich angestrebt haben?
Die Gründe dafür waren sicherlich vielfältig, jede finale Erklärung wird unzureichend sein, trotzdem wollen wir heute im Rückblick eine Analyse wagen. Zum einen überließen uns bereits 2013 die globalen Wettbewerber das Zukunftsfeld nicht einfach kampflos. Ein globaler Erfolg eines „deutschen" Konzepts war von Anfang an eine große Herausforderung zwischen dem schnellen Agieren der Großen (und trotzdem Schnellen) aus dem Silicon Valley und der schieren Investitions-Power Chinas, einem Land, das nicht mehr nur verlängerte Werkbank sein wollte.
So investierten z. B. 2013 die USA unter der Obama-Administration allein für die Produktionsforschung 1,6 Mrd. Euro und bereits 2012 starteten Programme wie das „Advanced Manufacturing Partnership". Im Rahmen dieses Programms wurden regionale Kompetenzzentren im Bereich Fertigung eingerichtet, um die an den Universitäten entwickelten Zukunftstechnologien auch in der Praxis einsetzen zu können.
Diese Programme ergänzen forschungsseitig, was industrieseitig durch das IIC und andere Netzwerke realisiert wurde. Neben General Electric und Cisco (Gründer des IIC) entdeckten zudem die Marktführer des Silicon Valleys zunehmend die Industrie als Betätigungsfeld (es fing alles klein an, z. B. mit der Akquisition von NEST- und einigen Roboter-Firmen durch Google).

Produktionsmaschinen, die das Twittern lernen siehe Beitrag (Bild: istockphoto)
Lange Zeit wurden die Player aufgrund ihrer Herkunft aus dem Consumer-Bereich von den etablierten Herstellern verdrängt, obwohl bei Google, Apple und anderen früh die Ambition in Richtung Industrie erkennbar war. „Software frisst den Rest der Welt" verkündete Marc Andreessen schon viele Jahre zuvor und er meinte damit nicht nur den Consumer-Bereich.
Schon im Jahr 2014 kamen daher auch wichtige Zukunftsimpulse wie die „twitternden" Produktionsmaschinen (auf Basis von MTConnect) aus den USA. Als in Deutschland noch die Standardisierungsgremien tagten, wurden aus den USA kommend de facto also bereits wichtige „Claims" besetzt. Dass Deutschland in den Jahren zuvor Schlüssel-Kompetenzen z. B. im Bereich der mobilen Kommunikation (Siemens) abgebaut hatte, war dabei sicherlich nicht hilfreich.
Auch China und der Rest der Welt waren aber nicht untätig und so gingen nicht nur Google & Co auf Einkaufstour. China plante 2014 für drei Jahre für die Modernisierung und Transformation der chinesischen Industrie mit Investitionen von 1,2 Billionen Euro. China wollte nicht länger nur die verlängerte Werkbank sein. Aus dem alten „Made in China" sollte nun „Created in China" werden.
Dass China in den folgenden Jahren führende deutsche, mittelständische Unternehmen aufkaufte, war da nur konsequent. So warnten 2014 auch bereits international agierende Vordenker wie Professor Sachsenmeier vor den Mythen der Industrie 4.0 und führten in Bezug auf China aus in einem Interview mit der Competence Site aus:
„In China wird sich Quantität zunehmend zu Qualität verwandeln, einfach, weil die Beschäftigung mit Produktion zu immer besseren Kenntnissen führt. Da diese Kenntnisse anderswo abgebaut werden, werden viele industrielle Bereiche Chinas über Zeit zu weltweit führenden Exzellenzclustern werden. Hochflexible Massenfertigung zeichnet China heute schon aus; das fokussierte Herstellen von Sonderanfertigungen ist da nicht weit."
International agierende Experten wie er warnten zudem davor, neben den USA und China andere Player zu vernachlässigen. Indien war schon damals als Markt und Informatikpool enorm wichtig. 2014 alarmierte Sachsenmeier daher zukunftsweisend in dem Interview mit der Competence Site:
„Dort werden Produkte und Dienstleistungen für hunderte von Millionen Menschen hergestellt... zu unschlagbaren Konditionen. Die damit verbundenen Lernkurven machen Indien wettbewerbsstark, wir werden es nur nicht gleich merken."
Damit war der eigene Erfolg für das deutsche Projekt „Industrie 4.0" im globalen Wettbewerb zumindest kein Selbstläufer. Es war von vorneherein klar, dass andere nicht nur zuschauen würden.
Zum anderen scheiterte Deutschland aber an hausgemachten Problemen. Was aber genau lief schief? In erster Linie scheiterte Deutschland an den Herausforderungen der deutschen Innovations-DNA und strategischen Weichenstellungen.
Unvermeidbare Herausforderungen der deutschen Innovations-DNA waren:
• Die zu geringe Marktorientierung:
Forschung („Theorie") vs. Markterfolge („Umsatz")
• Die zu geringe Nachfrageorientierung:
Angebotsorientierung (neue Lösung) vs. Nachfrageorientierung (wofür?)
• Die zu ausgeprägte Komplexitäts-Neigung
Kompliziert („ganzheitlich") vs. einfach („KISS")
Strategische Weichenstellungen (de facto) gegen den Zukunftserfolg waren:
• Das falsche Paradigma:
Basistechnologie („RFID", „Google Glass", „IP") statt integrierte Systeme
• Die unzureichende Differenzierung:
Kein spezifisch „deutscher" Fokus! (z. B. Kollaboration statt Konkurrenz)
• Das ungenutzte Mittelstands-Potenzial:
Leuchttürme statt Breite des Mittelstands
Zu den Herausforderungen der deutschen Innovations-DNA:
Es scheint dem „deutschen Wesen" inhärent, dass wir tief bohren und neue, technisch anspruchsvolle Lösungen kreieren wollen. Das macht den Wettbewerb schwer mit Wettbewerbern, die ihren Markt und Markterfolg in den Vordergrund stellen und mit smarten Lösungen schnell voraus- oder nachlaufen.
So wird dann in Deutschland MP-3 entwickelt, aber erst in den USA wird die entsprechende Technologie auf der Basis neuer Geschäftsmodelle zum Milliardengeschäft. Die ersten drei Probleme sind also typisch „deutsch" bzw. Teil unserer deutschen Innovations-DNA, die uns andererseits oft nachhaltige, komplexe Lösungen schaffen lässt. Hiermit müssen wir also in gewisser Weise auch zukünftig leben.
Zu den strategischen Weichenstellungen gegen den Zukunftserfolg:
So wie die ersten drei Problemfelder fast zwangsweise unseren Erfolg erschwerten, hätten wir in den letzten drei Problemfeldern mit unseren „typisch" deutschen Voraussetzungen punkten können, wenn de facto die richtigen Weichenstellungen erfolgt wären.
Dabei waren prinzipiell diese Weichenstellungen bereits im Abschlussbericht vorhanden. Die tatsächlichen Weichenstellungen erfolgten dann aber durch die „real existierenden" Forschungs- und Förderungsschwerpunkte und die öffentliche Wahrnehmung des Projekts Industrie 4.0.
Betrachtet man die Gründer des IIC wie Intel oder CISCO, so stehen diese globalen Marktführer vor allem für Basistechnologien wie Computer-Chips und Netzwerke. Deutschlands erfolgreichstes IT-Unternehmen, SAP, war vor allem deshalb erfolgreich, weil die Gründer eine integrierte Unternehmenssoftware realisierten, mit der die früheren Insellösungen überwunden wurden.
Siemens punktete in seiner Historie auch immer wieder durch integrative Lösungen. Und auch sonst hatten Lösungen aus Deutschland insbesondere im Bereich der ERP-, MES- und APS-Systeme oft eine besondere „integrierende" Kompetenz.
Dabei sind „integrative" Lösungen nicht nur auf den unteren produktionsnahen Ebenen gefordert, sondern auch auf den höheren, planerischen Ebenen bzw. in der Vernetzung aller Ebenen.
Bei aller Begeisterung für RFID-Chips, Google Glass oder Kameras an Lagerbehältern: Oft steckt der Return on Investment der Industrie 4.0 eben eher in den vielen noch nicht genutzten Potenzialen einer besseren Prozess- und Planungsvernetzung als in den einzelnen Basistechnologien, die dafür vor allem Enabler sein sollten (und nicht technologischer Selbstzweck). Trotzdem wurde insbesondere in der öffentlichen Wahrnehmung zu wenig Integration und Planung betont, sondern eher die leichter kommunizierbaren technischen Lösungen.
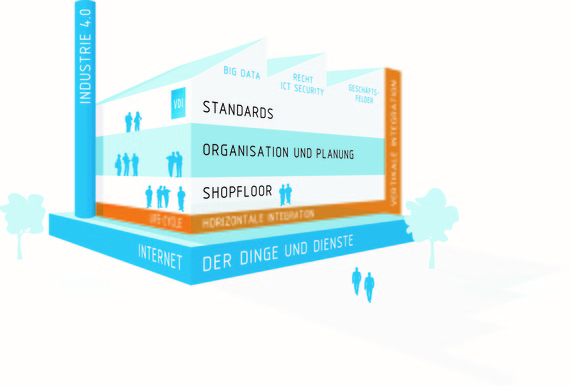
Haus der Industrie 4.0 des VDI, siehe VDI-Blog (Bild: VDI)
Dieses „Technologie-zentrierte" Paradigma war dabei keineswegs alternativlos. So betonte beispielsweise das VDI-Haus eine integrierte Sicht auf Industrie 4.0 und mit der „Aachener Perspektive" der Kollaborationsproduktivität existierte paradigmatisch durchaus eine andere Herangehensweise an das Thema Industrie 4.0. Am FIR an der RWTH Aachen wurden frühzeitig der ROI und die Produktivität betont, die aus einer besseren Kollaboration durch Vernetzung und Integration dezentraler Intelligenz entstehen.
Man hätte dann global Basiskomponenten (China) und Kommunikations- und Computer-Infrastruktur (Intel, CISCO, ..., USA) nutzen und nachhaltig eine eigene integrative Wertschöpfungskompetenz ergänzen können.
Solche und andere Kollaborations- und Netzwerk-Paradigmen waren aber als Leitbilder nicht ausreichend prägend. Dabei wären gerade solche integrativen, kollaborativen Industrie-4.0-Paradigmen auch kompatibler mit unserer „deutschen" ökonomischen DNA der sozialen Marktwirtschaft gewesen. Deutschland steht in besonderer Weise für eine Ökonomie des Miteinanders, die Kooperations- statt reinem Konkurrenz-Denken betont.
Deshalb sind kooperative Strukturen wie Verbände so wichtig und so erfolgreich in Deutschland. Auf dieser Basis hätten wir unsere ökonomische DNA für eine Differenzierungsstrategie in Richtung eines Paradigmas Industrie 4.0 = höherer ROI durch bessere Integration und Kooperation nutzen können.
Mit dieser Perspektive wäre die „deutsche" Industrie 4.0 mehr gewesen als nur die in Deutschland angesiedelten Bemühungen bzw. der deutsche Begriff für Smart Factories bzw. Cyber Physical Systems. So aber fehlte die wichtige Differenzierung.
Gerade mit einer solchen differenzierenden Strategie hätten wir dann auch noch breiter bei den eigentlichen Trägern des deutschen Wirtschaftswunders punkten können, den mittelständischen Unternehmen.
Integrierte, kooperative Systeme für eine bessere Produktion und ein besseres Produktionsmanagement, das wäre ein spezifischer Fokus für die deutsche Rolle in der Digitalisierung der Industrie gewesen, die auch im Mittelstand populärer gewesen wären als ein technologischer Selbstzweck mit unklarem ROI.
Zugleich hätte man den Mittelstand mit Reifegrad- und Vorgehensmodellen da abholen müssen, wo er stand. Oft weist der Mittelstand bis heute noch nicht den Organisationsgrad und die Basis-Digitalisierung auf, die für eine Hightech-Version der Industrie 4.0 notwendig wären.
Bis heute sind viele Baustellen im Bereich Organisation, Prozesse und Planung zu suchen. Erst dann kann durch letzte Optimierungen der Basistechnologien gepunktet werden. Durch den Fokus auf führende Leuchttürme und Hightech-Lösungen wurde aber die Chance verpasst, unsere Stärke des Mittelstands in der Breite zu nutzen.
Leider wurden 2013, 2014, ... diese Fragen nach dem nachhaltigen Erfolg zu wenig beleuchtet. Jetzt sind wir im Jahr 2020 klüger und in Trauer. Vielleicht finden wir aber nun unseren Weg in den kommenden Jahren ohne ein nationales Label, aber mit spezifisch deutscher Kompetenz.
Wenn wir unsere DNA erkennen und die richtigen strategischen Weichenstellungen (richtiger Fokus, u. a. Marktorientierung, richtiges Paradigma, Mittelstandsorientierung, ...) vornehmen, dann sollte uns in Zukunft der Erfolg gelingen, selbst ohne einen nationalen Begriffsrahmen.